Unlock the Magic of FDM 3D Printing: Discover Its Amazing Features and Benefits!
FDM 3D printing, or Fused Deposition Modeling, has transformed the landscape of manufacturing, design, and even art. This technology has gained traction in various industries due to its affordability, ease of use, and versatility. As more individuals and businesses recognize its potential, the popularity of FDM 3D printers continues to soar. This article aims to explore the fascinating features, diverse uses, and significant benefits of FDM 3D printers, shedding light on why they are becoming indispensable tools in today’s world.
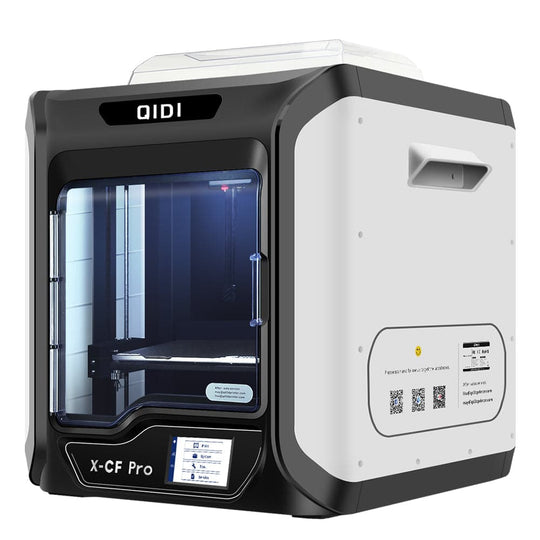
Understanding FDM 3D Printing Technology
The fundamental principle behind FDM technology is relatively straightforward: it constructs objects layer by layer. This process begins with feeding a thermoplastic filament into a heated nozzle, where it melts and is then extruded onto a build platform. As the material cools, it solidifies, forming a tangible object. This layer-by-layer method allows for intricate designs and complex geometries that are often challenging to achieve through traditional manufacturing techniques. Common materials used in FDM printing include PLA, ABS, and PETG, each offering unique properties suited for different applications. A friend of mine, who runs a small prototyping business, often shares how the ability to quickly print prototypes has revolutionized their workflow, allowing for faster iterations and improved designs.
Key Features of FDM 3D Printers
FDM 3D printers come packed with features that cater to both beginners and experienced users. One of their most appealing aspects is their user-friendly nature; many models are designed with intuitive interfaces and easy setup processes. Furthermore, these printers support a wide variety of materials, enabling users to select the best filament for their specific needs. Another standout feature is the ability to create complex geometries, which opens up endless possibilities for innovation. From large prints suited for industrial applications to small, detailed items for hobbyists, FDM printers offer a broad range of print sizes, accommodating projects of various scales. A colleague of mine, who is a passionate hobbyist, often showcases how he utilizes his FDM printer to create intricate miniatures for tabletop games, emphasizing the printer's versatility and precision.
Applications and Uses of FDM 3D Printing
The applications of FDM 3D printing are as diverse as the technology itself. In the world of prototyping, designers can quickly turn digital concepts into physical models, allowing for faster feedback and iterative improvements. Educational institutions are also embracing this technology; students can engage in hands-on learning by creating projects that inspire creativity and problem-solving. In healthcare, FDM printers are used to produce customized prosthetics and anatomical models, improving patient outcomes through tailored solutions. Manufacturing industries leverage FDM printing for creating tooling, fixtures, and even end-use parts, significantly reducing production times and costs. For instance, an engineering firm I know recently implemented FDM technology, leading to a dramatic speedup in their prototyping phase, ultimately enhancing their product launch timelines.
Benefits of Using FDM 3D Printers
FDM 3D printing offers numerous advantages that make it a go-to choice for many. One of the primary benefits is cost-effectiveness; the materials used are generally affordable, and the ability to produce items on-demand reduces the need for large inventories. Rapid prototyping capabilities allow designers to quickly test and refine their ideas, fostering innovation and creativity. Moreover, FDM printing significantly reduces waste compared to traditional manufacturing methods, as it only uses the material necessary to create each object. Customization is another benefit, enabling users to create tailored solutions that meet specific requirements. As a result, companies can respond more effectively to market demands and customer preferences. A friend who operates a small business has shared how FDM printing has allowed them to offer personalized products, leading to greater customer satisfaction and loyalty.
Challenges and Considerations
While FDM printing boasts many advantages, it is not without challenges. Print quality can sometimes be an issue, particularly with complex designs, and users may encounter material limitations that affect the durability or appearance of the final product. However, these challenges can often be addressed through proper calibration, maintenance, and the use of high-quality filaments. Additionally, staying updated with the latest printing techniques and software can significantly enhance the overall printing experience.
Final Thoughts on FDM 3D Printing
In summary, FDM 3D printing technology has unlocked a world of possibilities across various fields, from prototyping to healthcare and beyond. Its unique features, broad range of applications, and significant benefits make it an invaluable tool for individuals and businesses alike. As this technology continues to evolve, the potential for innovation remains limitless. I encourage readers to explore the wonders of FDM 3D printers and consider how they might enhance their own projects or professional pursuits.