Unlock the Secrets of Professional-Grade 1.75mm ABS Filament for Stunning 3D Prints!
When embarking on the journey of 3D printing, the choice of filament is crucial to the success of your projects. Among the myriad of materials available, professional-grade 1.75mm ABS filament stands out for its popularity and versatility. This thermoplastic is favored by hobbyists and professionals alike due to its robust properties and ability to produce high-quality prints. Whether you’re creating intricate prototypes, functional parts, or artistic designs, understanding the capabilities of ABS filament can significantly enhance your 3D printing experience.
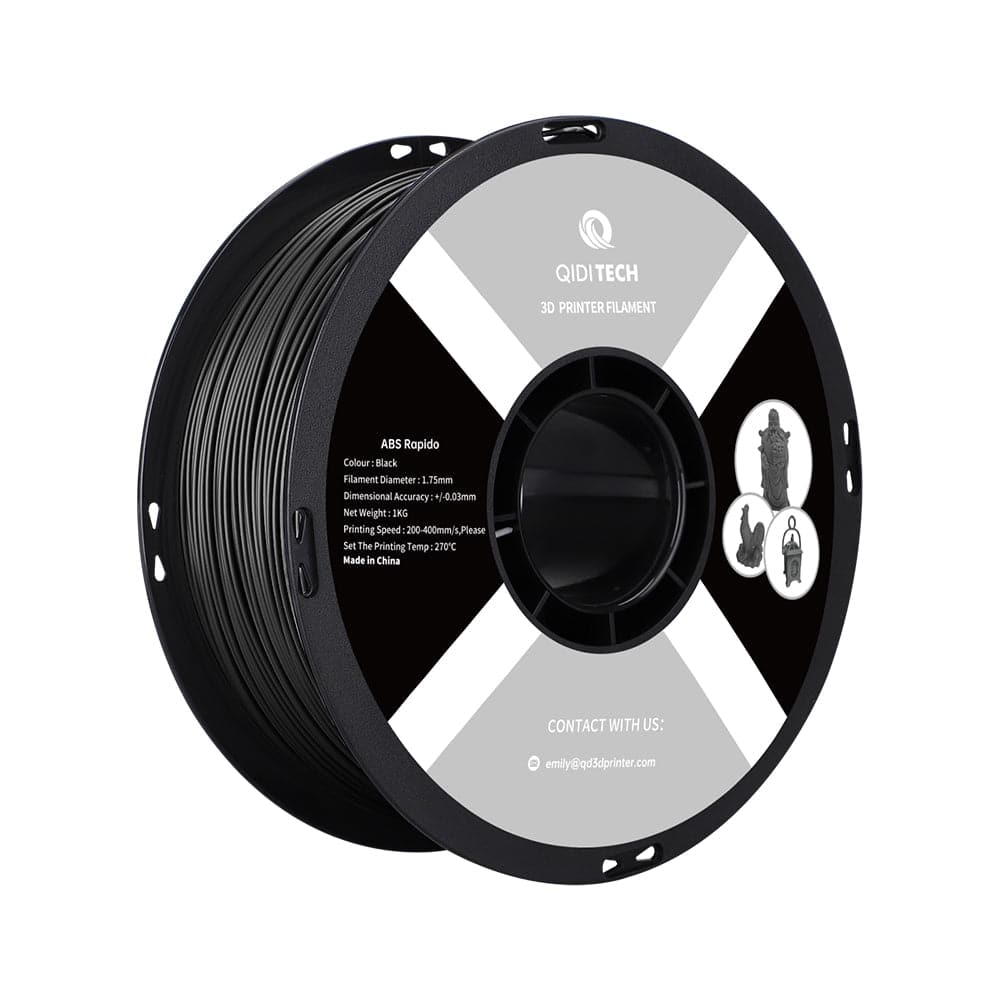
Understanding ABS Filament
ABS, or Acrylonitrile Butadiene Styrene, is a thermoplastic polymer known for its durability and strength. The chemical composition of ABS includes three primary components: acrylonitrile, butadiene, and styrene, each contributing unique properties to the filament. This combination results in a material that is not only tough but also resistant to impact and heat, making it ideal for 3D printing applications. ABS filament is particularly advantageous in situations where strength and resilience are paramount, allowing for the production of parts that can withstand everyday wear and tear. The ability to be molded and shaped also enables the creation of intricate designs that maintain their structural integrity.
Key Properties of 1.75mm ABS Filament
Professional-grade 1.75mm ABS filament boasts a range of properties that distinguish it from other materials. One of the standout features is its flexibility, which allows for the creation of models that can bend without breaking. This flexibility is complemented by excellent impact resistance, making ABS an excellent choice for functional prototypes or parts that may encounter stress during use. Additionally, dimensional stability ensures accurate reproductions of the intended designs, a critical factor for professional applications. The combination of these properties not only enhances the quality of the printed objects but also increases their usability in real-world applications, ensuring that they perform as expected.
Applications of Professional-Grade ABS Filament
The applications of 1.75mm ABS filament are vast and varied, spanning across numerous industries. In prototyping, for instance, its durability and ease of printing make it a preferred material for creating functional models that can be tested and refined. The automotive industry frequently utilizes ABS in the production of dashboard components and other interior parts, where strength and aesthetic appeal are crucial. Additionally, consumer products such as toys and household items benefit from ABS's robustness and ability to be easily painted or finished. A friend of mine recently used ABS filament to create a custom case for a drone, highlighting how this material can be tailored to specific needs while ensuring both functionality and style.
Best Practices for Using 1.75mm ABS Filament
To make the most of your professional-grade 1.75mm ABS filament, it’s essential to follow best practices during the printing process. Proper printer settings are critical; maintaining an adequate nozzle temperature (typically between 220°C and 250°C) ensures optimal flow and adhesion. Bed adhesion can be a challenge with ABS, so using a heated bed set to around 80°C to 110°C can significantly improve success rates. Techniques such as applying a glue stick or using blue painter's tape can also enhance adhesion. Post-processing methods, such as sanding and acetone vapor smoothing, can elevate the final appearance of your prints, giving them a polished look. Common challenges include warping and stringing; however, adjusting print speed and environmental factors can help mitigate these issues.
Maximizing the Potential of ABS Filament
In summary, professional-grade 1.75mm ABS filament is a versatile and reliable choice for creating stunning 3D prints. With its superior properties, including durability, flexibility, and dimensional stability, ABS filament excels in a variety of applications ranging from prototyping to consumer products. By following best practices and understanding the material’s unique characteristics, you can unlock the full potential of ABS in your 3D printing endeavors. I encourage you to explore the world of ABS filament for your next project, as the results can be both impressive and satisfying.