Unlock the Secrets of ABS Filament: Transform Your 3D Printing Game!
In the vibrant world of 3D printing, materials play a crucial role in determining the quality and functionality of printed objects. One of the most popular choices among enthusiasts and professionals alike is ABS filament. Acrylonitrile Butadiene Styrene, or ABS, is a thermoplastic that has become synonymous with durability and versatility in the 3D printing community. From creating intricate prototypes to robust consumer products, ABS filament offers a range of applications that highlight its significance. In this article, we’ll dive deep into the properties of ABS filament, its diverse uses, best practices for 3D printing, and how to tackle common challenges that may arise during your printing journey.
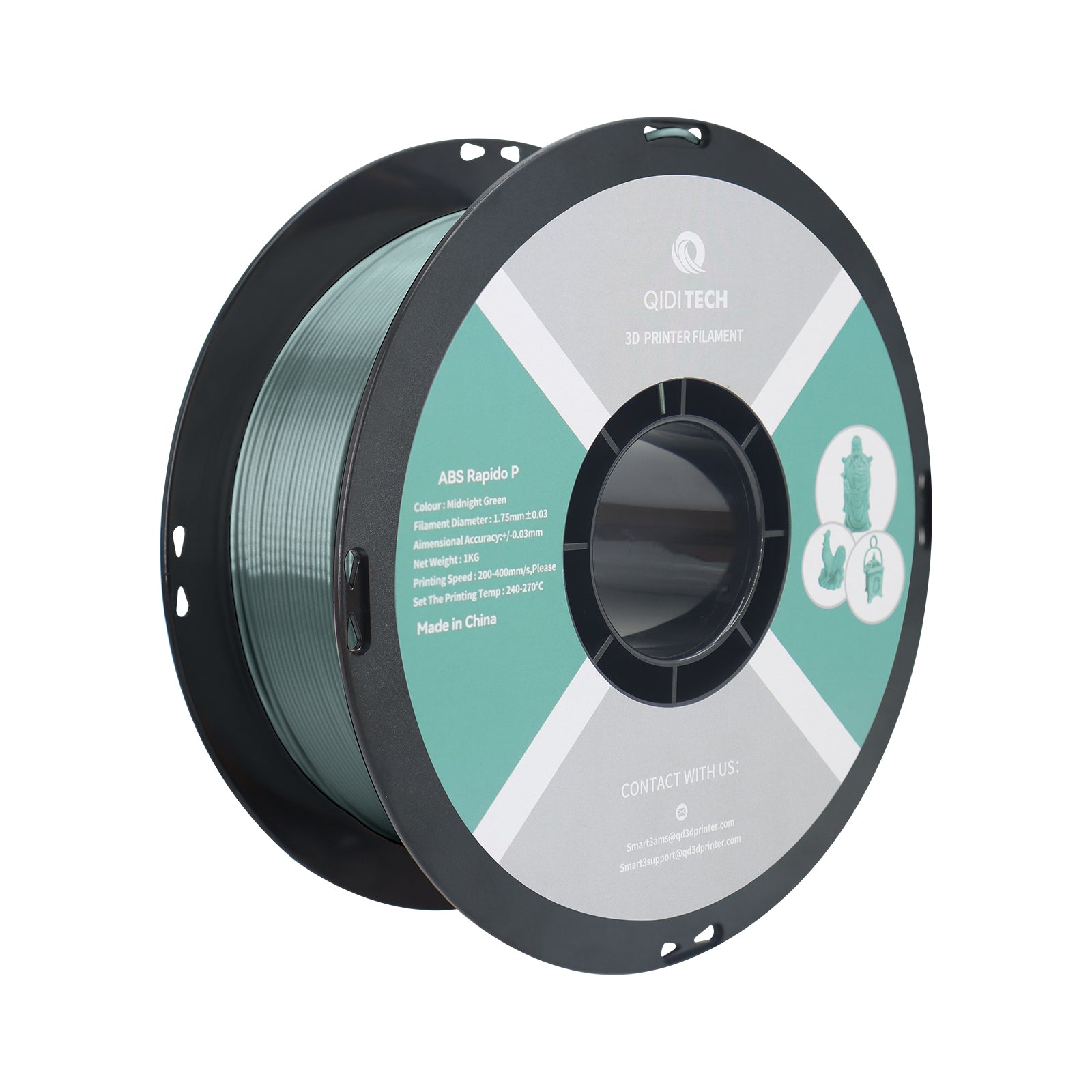
Understanding ABS Filament
ABS filament is composed of three main components: acrylonitrile, butadiene, and styrene. This unique blend gives ABS its remarkable properties. First off, ABS is known for its impressive strength, making it ideal for functional parts that require durability. It can withstand impact and stress better than many other 3D printing materials, which is why it's often favored in engineering and design applications.
Another key characteristic of ABS is its flexibility. Unlike more brittle materials, ABS can bend and flex under pressure, reducing the likelihood of breakage during use. This makes it perfect for parts that need to endure movement or slight deformation without failing. Heat resistance is another significant property; ABS can withstand higher temperatures compared to PLA, making it suitable for applications that might expose the printed object to warmth or heat.
However, it’s essential to note that the properties of ABS filament can vary based on the specific formulation and color additives used. For instance, some ABS variants may offer improved layer adhesion or enhanced UV resistance. This diversity allows users to select the right type of ABS filament tailored to their specific project needs, ensuring optimal performance and results.
Applications of ABS Filament
ABS filament boasts a wide range of applications across various industries. One of the most prominent sectors using ABS is automotive manufacturing. Many automotive prototypes and even some production parts are made from ABS due to its strength and ability to tolerate temperature fluctuations. Friends of mine who work in the automotive industry have shared stories about how ABS allows them to create durable and lightweight components that are essential for modern vehicles.
In addition to automotive uses, ABS filament is prevalent in consumer products. Items such as toys, household goods, and electronic enclosures often utilize ABS due to its resilience and finish quality. For instance, many popular toys are manufactured using ABS because it can be easily molded into complex shapes while remaining tough enough to withstand wear and tear from play.
Prototyping is another area where ABS shines. Designers and engineers rely on ABS for creating functional prototypes that mimic the final product's properties. ABS allows for quick iterations during the design process, facilitating rapid prototyping that enables teams to test and refine their ideas efficiently. The ability to create prototypes that can endure real-world conditions makes ABS a go-to choice for many professionals.
Best Practices for 3D Printing with ABS Filament
When it comes to 3D printing with ABS filament, achieving the best results requires attention to detail and adherence to specific practices. First and foremost, it's crucial to ensure that your printer's bed is properly prepared. Ideally, the print bed should be heated to around 100°C to minimize warping during the printing process. Some users even apply a layer of glue stick or Kapton tape to further enhance adhesion.
Printer settings also play a vital role in the outcome. A nozzle temperature between 220°C and 250°C is typically recommended for ABS filament. It's essential to experiment within this range to find the optimal temperature for your specific filament brand and printer setup. Additionally, using an enclosure for your printer can help maintain a stable temperature and reduce the risk of warping and cracking.
Post-processing techniques can greatly enhance the final appearance of your ABS prints. For instance, sanding can smooth out any rough edges, while acetone vapor smoothing can give your prints a glossy finish. A friend of mine recently used this technique on a prototype he made, and the results were stunning, transforming a rather rough print into a professional-looking piece.
Common Challenges and Solutions
Despite its many advantages, printing with ABS filament does come with challenges. One of the most common issues faced by users is warping, which occurs when the layers of the print cool unevenly, causing the object to lift from the print bed. This can be mitigated by ensuring a properly heated print bed and using an enclosure to maintain temperature stability.
Another concern is the fumes emitted during the printing of ABS. These fumes can be unpleasant and potentially harmful, making proper ventilation crucial. Using an air purifier or printing in a well-ventilated area can help alleviate this issue. Some individuals even choose to install fume extraction systems for a safer printing environment.
Final Thoughts on ABS Filament in 3D Printing
In summary, ABS filament stands out in the 3D printing landscape due to its strength, flexibility, and heat resistance, making it a favorite among various industries. Its diverse applications range from automotive parts to consumer products and prototyping, showcasing its versatility. By understanding the properties, best practices, and challenges associated with ABS filament, you can elevate your 3D printing projects to new heights. Whether you're a seasoned professional or just starting, experimenting with ABS filament can lead to innovative creations and remarkable results.