Unleashing the Power of Giant 3D Printers: Discover Their Amazing Features and Game-Changing Applications!
In recent years, the landscape of manufacturing and production has undergone a dramatic transformation, largely driven by the advancements in 3D printing technology. Among these innovations, big 3D printers have emerged as powerful tools that are reshaping various industries. But what exactly constitutes a big 3D printer? These machines, often characterized by their substantial build volumes and advanced capabilities, are making waves in sectors ranging from aerospace to healthcare. This article aims to explore the defining features of giant 3D printers and their myriad applications, revealing how they are not just tools, but catalysts for change in the way we think about production and design.
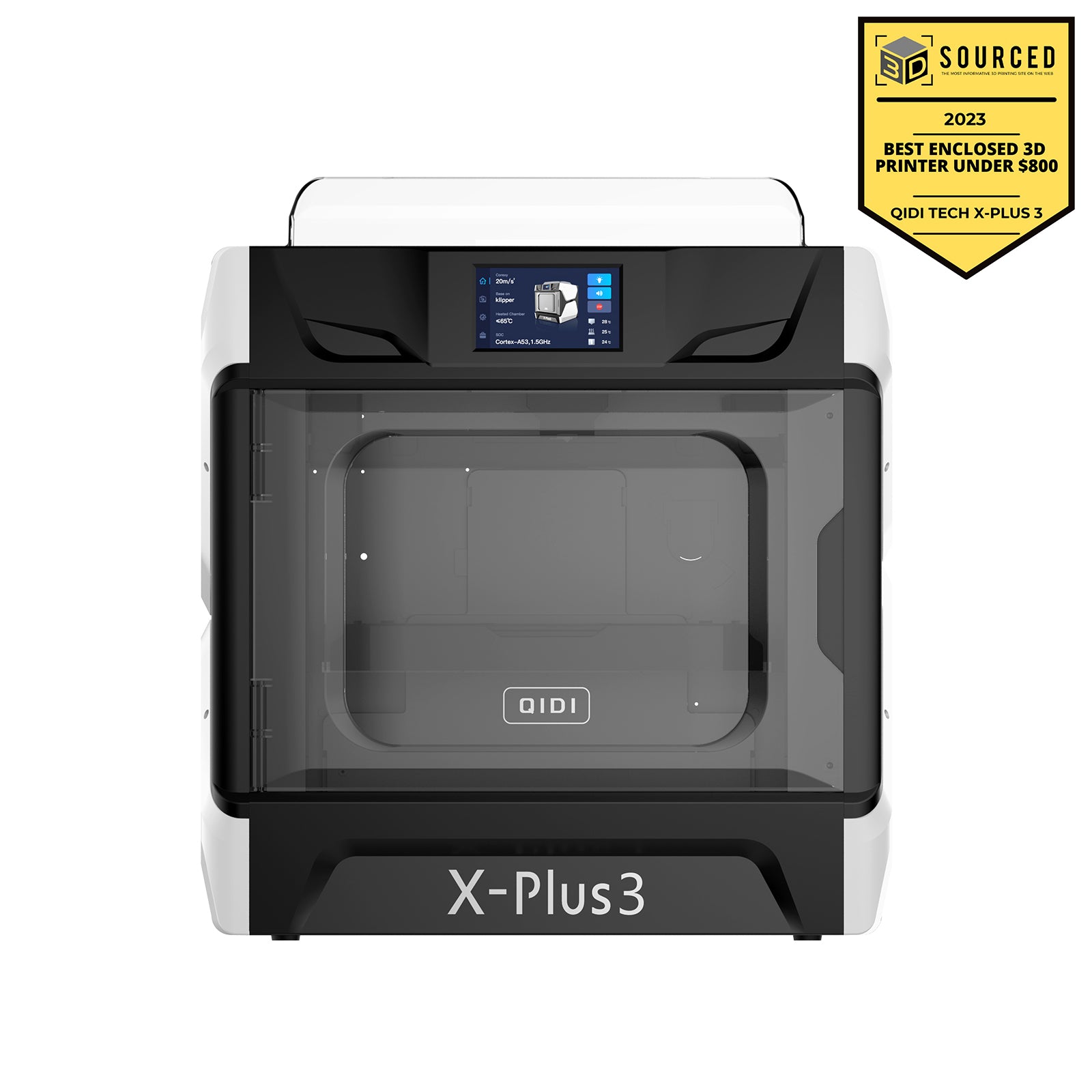
What Constitutes a Big 3D Printer?
When we refer to a "big" 3D printer, we typically mean a machine that boasts a significant build volume—often defined as having a printing area exceeding 1 cubic meter. These printers are capable of producing large-scale components that smaller printers simply cannot achieve. The different types of big 3D printers include industrial-grade machines, which are often used in manufacturing environments, and large-format printers that cater to more specialized applications. For instance, some big 3D printers use additive manufacturing techniques that allow for the production of large parts in one piece, eliminating the need for assembly and reducing the risk of errors. Through the combination of size and advanced technology, big 3D printers stand out as indispensable assets in modern manufacturing landscapes.
Features of Giant 3D Printers
The key features that distinguish big 3D printers go beyond just their size. First and foremost is their impressive build volume, which allows manufacturers to create substantial parts in a single print. Additionally, many of these printers offer compatibility with a wide range of materials, including plastics, metals, and composites, enabling the production of diverse products. Speed is another critical feature; advancements in printing technology have led to faster printing rates without compromising quality. Precision is paramount in 3D printing, and big printers often incorporate sophisticated software and hardware to ensure that each layer is accurately deposited. Furthermore, features like multi-material printing capabilities and automated calibration systems are becoming increasingly common, enhancing the overall usability and efficiency of these giant machines. With each advancement, big 3D printers are pushing the boundaries of what is possible in additive manufacturing.
Material Versatility
One of the most significant advantages of big 3D printers is their versatility in terms of materials. They can handle a diverse range of substances, including thermoplastics, metals such as titanium and aluminum, and advanced composites that combine the properties of multiple materials. This material versatility allows companies to tailor their products for specific applications, whether it be the lightweight yet strong components required in the aerospace industry or the biocompatible materials needed for healthcare devices. The choice of material not only impacts the physical properties of the final product—such as strength, flexibility, and weight—but also influences the overall cost and production time. As a result, the ability to work with various materials makes big 3D printers a game-changer in many sectors.
Applications of Big 3D Printers
The applications of big 3D printers are as diverse as the industries they serve. In the aerospace sector, for instance, they are used to produce lightweight parts that enhance fuel efficiency without sacrificing safety. The automotive industry benefits from rapid prototyping capabilities, allowing manufacturers to create and test new designs quickly. In construction, giant 3D printers are being employed to print entire architectural structures, minimizing waste and reducing labor costs. Healthcare is another field where these printers shine; they are utilized to create custom prosthetics and implants tailored to individual patients. The ability to produce complex geometries and structures that would be impossible with traditional manufacturing methods not only saves time but also opens up new possibilities for innovation.
Impact on Manufacturing and Prototyping
The impact of big 3D printers on manufacturing and prototyping cannot be overstated. They are revolutionizing the way products are designed, tested, and manufactured. By significantly reducing production times and costs, these printers allow companies to bring products to market faster and more efficiently. For instance, a friend of mine who works in automotive prototyping shared how his team can now create complex prototypes in days instead of weeks, allowing for quicker iterations and refinements. The ability to produce on-demand parts also reduces inventory costs and waste, making manufacturing processes more sustainable. As industries continue to embrace these technologies, the potential for new applications and innovations only grows.
Key Takeaways on Big 3D Printers
In summary, big 3D printers are not just large machines; they are transformative tools that are changing the landscape of manufacturing and design across multiple industries. With their impressive features, including vast build volumes, material versatility, and speed, they are enabling companies to innovate and streamline their processes like never before. As we continue to explore the capabilities and applications of these giant printers, it becomes increasingly clear that they hold the potential to revolutionize production methods and redefine what is possible in the world of manufacturing. Embracing this technology could lead to significant advancements and efficiencies in the future, making it an exciting time for anyone involved in these fields.