Unlock the Secrets to Choosing the Perfect 3D Printing Slicer: Your Ultimate Guide Awaits!
3D printing has revolutionized the way we create and manufacture objects, and at the heart of this technology lies the 3D printing slicer. This essential software converts 3D models into instructions that a printer can understand, playing a pivotal role in determining the quality and success of your prints. Choosing the right slicer can enhance your printing experience, whether you are crafting intricate designs or simple prototypes. With a multitude of options available, understanding the nuances of different slicers is crucial to achieving the desired results. In this guide, we will delve into the world of 3D printing slicers, exploring their functionalities, features, and the key factors to consider when selecting the perfect one for your needs.
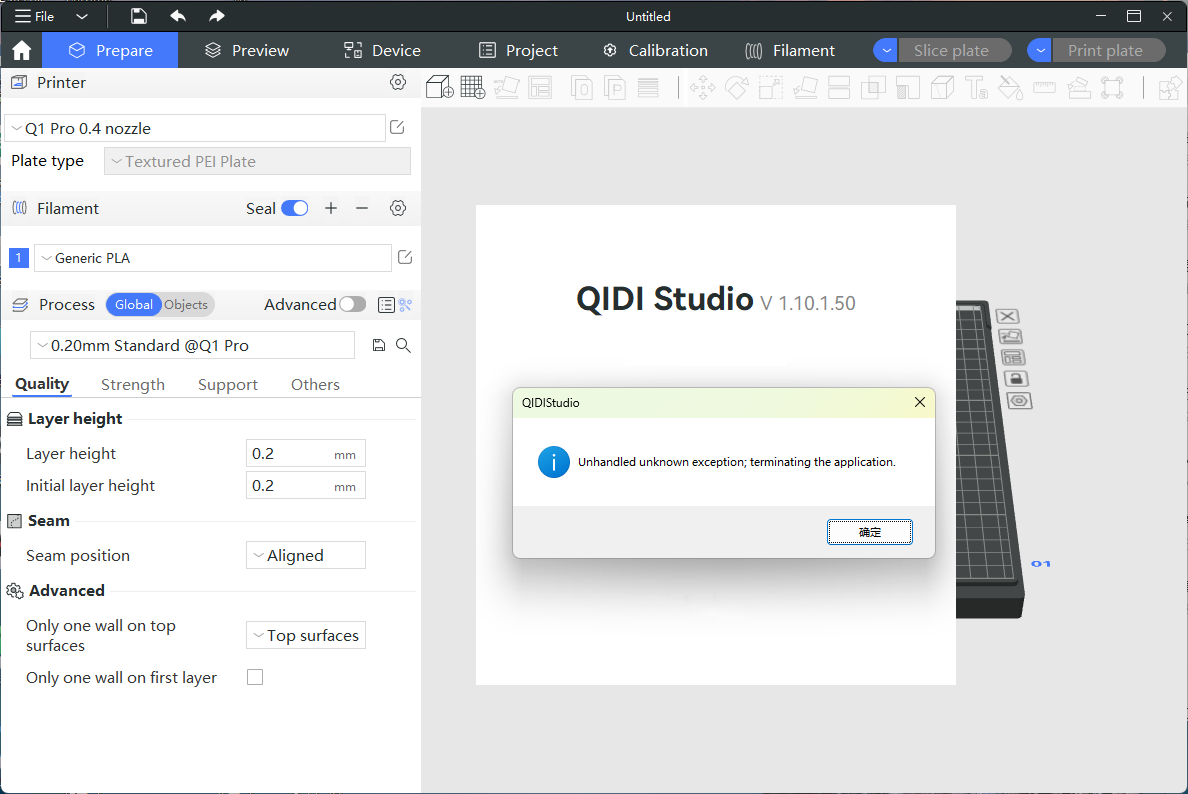
Understanding 3D Printing Slicers
A 3D printing slicer acts as the intermediary between your 3D model and the printer, translating digital designs into a series of precise movements for the printer's nozzle. This process involves slicing the model into horizontal layers, which the printer will then build upon one at a time. Different slicers come equipped with a variety of features that cater to diverse printing needs. Slicing speed is often a critical factor, as it can drastically affect the time it takes to complete a print. Additionally, compatibility with various printer types and supported file formats ensures that the slicer can handle the models you intend to print. User interface design also plays a significant role in usability; a well-designed interface can make the slicing process intuitive, especially for beginners, while advanced features may cater to experienced users seeking more control over their prints.
Key Factors to Consider When Choosing a Slicer
When selecting a 3D printing slicer, several critical factors should be at the forefront of your decision-making process:
- Compatibility with printer types: Ensure that the slicer is compatible with the specific type of 3D printer you own, whether it is FDM, SLA, or another technology.
- Supported file formats: Different slicers support various file formats. Make sure the slicer can handle the file types you plan to use, such as STL or OBJ.
- User experience and interface design: A user-friendly interface can significantly enhance your slicing experience, especially if you are new to 3D printing.
- Customization options: Look for slicers that offer customizable settings, allowing you to adjust parameters such as layer height and print speed to suit your needs.
- Community support and resources: Strong community support can be invaluable, providing forums, tutorials, and troubleshooting advice that can help you navigate challenges.
Each of these factors can influence your print quality, usability, and overall satisfaction with your 3D printing projects. As my friend learned the hard way when he purchased a slicer without checking compatibility, a mismatch can lead to frustration and wasted materials.
Comparing Popular 3D Printing Slicer Options
The market offers a variety of slicers, each with its strengths and weaknesses. For beginners, some slicers offer simplicity and ease of use, allowing users to start printing with minimal setup. These options typically have an intuitive interface, making it easy to navigate through the slicing process. However, they may lack advanced features that experienced users might seek, such as detailed control over print settings.
On the other hand, there are slicers designed for advanced users that provide robust features such as extensive customization options and fine-tuning capabilities. These slicers can significantly enhance performance metrics like speed and accuracy, but they may come with a steeper learning curve. Additionally, cost considerations are important; some slicers are free, while others may charge a fee for premium features. Evaluating the value they provide based on your skill level and printing needs is essential. A friend of mine who is an avid 3D printing hobbyist swears by a particular slicer for its advanced features, but he often recommends newcomers start with a simpler option before making the leap.
Tips for Optimizing Slicer Settings
To achieve the best print results, optimizing your slicer settings is crucial. Here are some practical tips to consider:
- Layer height and print speed: Adjusting the layer height can affect print quality and speed. Smaller layer heights can yield smoother finishes but may increase print time.
- Infill patterns and density: The infill pattern and density can influence the strength and weight of your print. Consider the purpose of your model when selecting these settings.
- Support structures and their configurations: When printing complex models, configuring support structures properly can prevent issues during the printing process. Experimenting with different support settings can lead to better outcomes.
My experience with optimizing settings has taught me that even small adjustments can make a significant difference in print quality. A friend once printed a delicate model that failed due to improper support settings; after tweaking them, he successfully printed it on the second attempt.
Making an Informed Choice for Your 3D Printing Journey
Choosing the right 3D printing slicer is a pivotal step in your 3D printing journey. By understanding the functionalities of different slicers and considering key factors such as compatibility, user experience, and customization options, you can make an informed decision that meets your unique needs. Moreover, experimenting with various slicer settings can enhance your prints and lead to exciting results. Remember, the world of 3D printing is vast, and finding the perfect slicer may require some trial and error, but the rewards are well worth the effort. Embrace the process, and happy printing!