Unlock Your 3D Printing Potential with This Must-Have Filament!
In the world of 3D printing, the filament you choose can make all the difference in the quality and durability of your finished product. One standout option that has captured the attention of both hobbyists and professionals is ABS filament. Known for its versatility and strength, ABS (Acrylonitrile Butadiene Styrene) has become a popular choice among users looking to create robust models and prototypes. Whether you're a seasoned 3D printing expert or a newcomer eager to explore the possibilities, understanding the benefits and applications of ABS filament can unlock your 3D printing potential. This article will guide you through the essentials of ABS filament, why it stands out in the market, and practical tips to get the most out of your 3D printing experience.
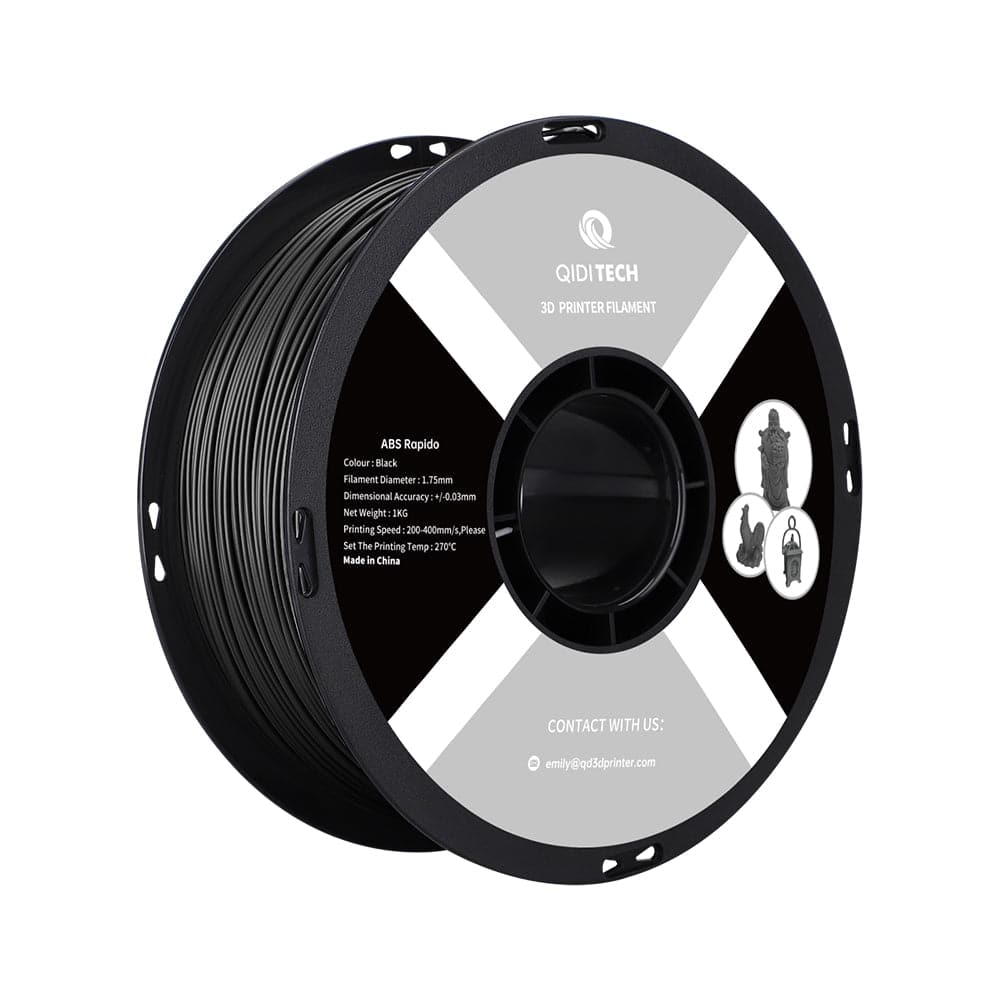
Understanding ABS Filament
ABS filament is a thermoplastic polymer known for its toughness and resilience. Composed of three main components—acrylonitrile, butadiene, and styrene—this filament offers a unique blend of properties that make it ideal for various 3D printing applications. One of the standout features of ABS is its durability; it can withstand significant impacts and is less likely to crack or break compared to other materials. Additionally, ABS has excellent heat resistance, making it suitable for items that may be exposed to elevated temperatures. This combination of strength and stability sets ABS apart as a premium choice for those looking to produce high-quality, long-lasting prints. Friends of mine who have dabbled in 3D printing often rave about ABS for their larger projects, noting that its resilience gives them the confidence to create without worrying about structural integrity.
Benefits of Using ABS Filament for 3D Printing
When comparing ABS filament to other popular materials like PLA (Polylactic Acid), several advantages come to light. One of the most significant benefits of ABS is its strength; it is much sturdier than PLA, making it ideal for functional parts and prototypes that require durability. Moreover, ABS filament is highly flexible, allowing for a degree of bend without breaking, which is particularly beneficial for items that may experience stress during use. Another notable advantage is its excellent post-processing capabilities. ABS can be easily sanded, painted, or even smoothed with acetone vapor, allowing makers to achieve a professional finish on their projects. A friend of mine who frequently creates custom toys for his kids swears by ABS filament, stating that it not only holds up to rough play but also allows him to refine the details for a polished look.
Applications of ABS Filament
The versatility of ABS filament makes it suitable for a wide range of applications. One of the primary uses is in prototyping, where designers and engineers can quickly create models to test functionality and fit. In the automotive industry, ABS is often used for producing parts like dashboards and interior components due to its durability and heat resistance. Additionally, consumer products such as toys, tools, and household items commonly utilize ABS for its strength and aesthetic versatility. For instance, a colleague of mine recently printed a custom phone holder using ABS, and the final product was not only sturdy but also visually appealing. The ability to create functional and attractive items with ABS filament is a major draw for many 3D printing enthusiasts.
Tips for Printing with ABS Filament
To achieve the best results when printing with ABS filament, several practical tips can help ensure success. First, it's essential to set your printer to the appropriate temperature; typically, ABS prints best at a nozzle temperature of around 210-250°C. Additionally, bed adhesion is critical; using a heated bed set between 80-100°C can help minimize warping, a common issue with ABS. Some users recommend applying a thin layer of glue stick or using specialized adhesives to further enhance adhesion. To combat warping, consider printing in an enclosed space to maintain a consistent temperature around your print. A friend who regularly prints with ABS swears by these techniques, noting that they have drastically improved his print quality and reduced failed prints.
Common Challenges and Solutions
Despite its many advantages, printing with ABS filament does come with challenges. One of the most prevalent issues is warping, which occurs when the material cools unevenly during printing, causing the edges of the print to lift. To mitigate this, ensuring that your bed is adequately heated and using proper adhesion techniques are key. Another consideration is the fumes emitted during printing; ABS can release unpleasant odors and potentially harmful vapors. To address this, it's advisable to print in a well-ventilated area or use an enclosure with a filtration system. By sharing these insights, my 3D printing group has successfully navigated the challenges associated with ABS, allowing us to focus on creativity rather than technical obstacles.
Maximizing Your 3D Printing Experience with ABS Filament
In summary, ABS filament is a powerhouse in the realm of 3D printing, offering durability, flexibility, and versatility that can enhance your projects significantly. From prototyping to creating functional consumer products, its applications are vast and varied. By understanding the benefits and employing effective printing techniques, you can make the most out of this exceptional material. Whether you are an experienced maker or just starting your 3D printing journey, considering ABS filament could be the key to unlocking a world of creative possibilities in your next project.